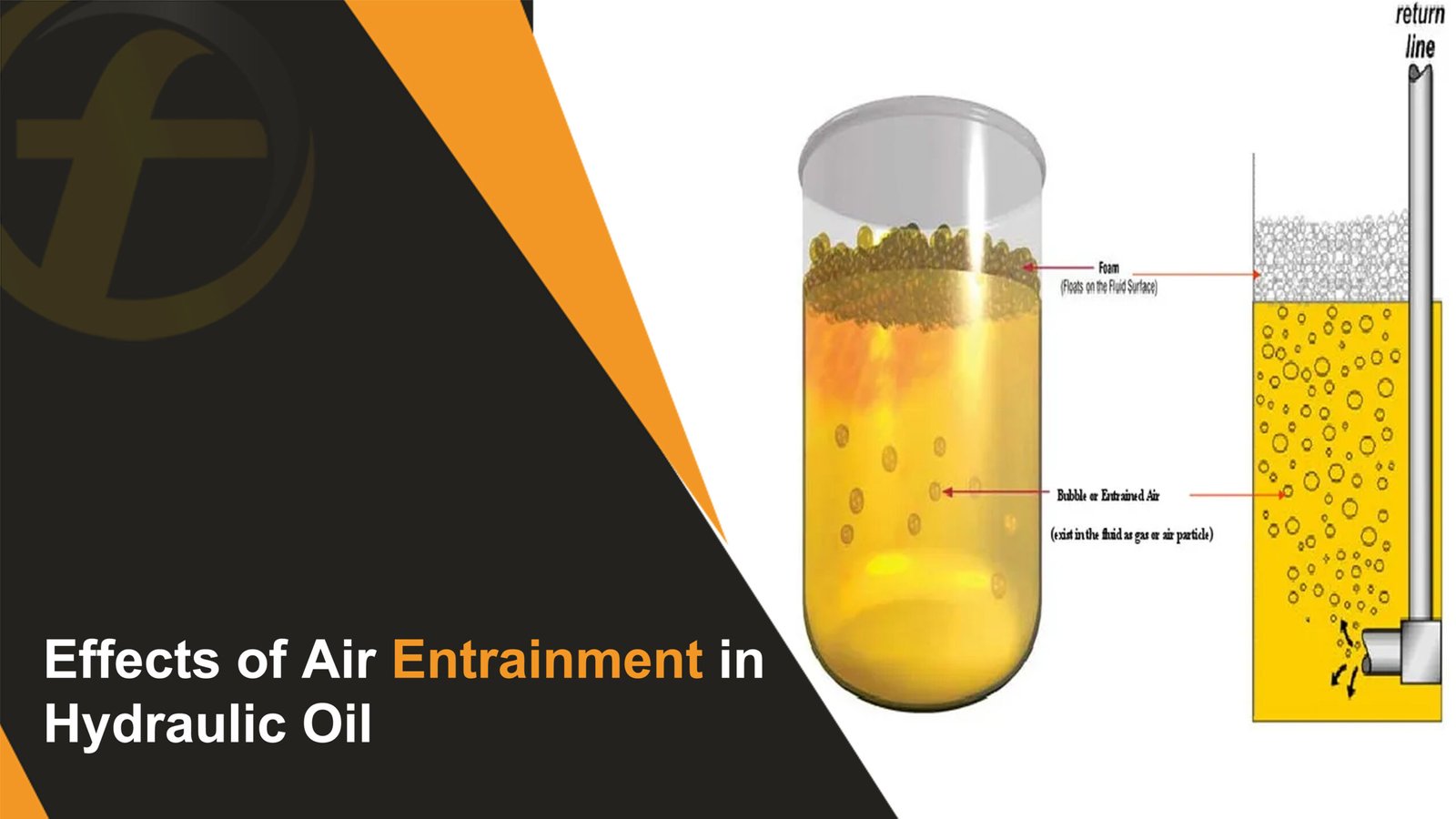
Hydraulic oil air can cause noise, damage, and overheating. The worst kind is tiny air bubbles mixed in with the oil, which can make the system work poorly. To prevent this, it’s essential to keep the system well-maintained, use the right oil, and ensure air doesn’t get trapped. This blog will discuss how air can get into hydraulic oil, why it’s a problem, and how to prevent it.
Understanding the Effects of Air Contamination on Hydraulic Systems
At Fubex Lubricants, contaminants can make hydraulic systems work poorly. A contaminant damages how well the system and its parts work. Air can get into hydraulic fluid in four ways:
- Dissolved Air – Hydraulic fluid usually has 6-12% air mixed in.
- Free Air – This is air trapped in pockets inside the system. It can be removed by filling parts correctly and bleeding the system when starting up.
- Foam – These are bigger air bubbles (larger than 1mm) at the top of the fluid. A little foam is usually harmless.
- Entrained Air – These are tiny air bubbles (less than 1mm) spread out in the fluid.
The worst kind of air is entrained air, which can cause problems like:
- Loud noises
- A “spongy” feeling when the system responds
- Thinner fluid, which can cause parts to wear out faster
- Extra heat
- Poor cooling of the system
- The fluid can break down, causing damage to parts, overheating, and burning seals
- Cavitation damage
- The system works less efficiently
Fixing air problems in the system is essential to keep it running smoothly and to help it last longer.
Cavitation Damage
Cavitation happens when bubbles quickly form and collapse in liquids because of pressure changes. It usually occurs when the liquid’s pressure drops fast, creating bubbles in low-pressure areas. When these bubbles move to higher-pressure areas, they collapse, creating a shockwave.
Cavitation causes a lot of damage to things like propellers and hydraulic equipment. It can even happen to fish fins as they swim! Fish fins can heal, but machines can’t!
Other signs of air in the system include:
- Loud or strange noise – This can happen because of aeration or cavitation. Aeration occurs when air mixes with the fluid, causing noise when the liquid is squeezed. Cavitation occurs when the fluid is too low, and air enters the system instead.
- High pressure occurs when hoses or pipes are too small to move enough fluid, causing air blockages. You can fix this by draining the system and using bigger hoses.
Up to 12% of hydraulic fluid usually contains dissolved air, which can escape and cause air bubbles to form. This is called gaseous cavitation.
How Hydraulic Fluid Bubbles Form
Air bubbles can form in hydraulic fluid for different reasons. Here are some common causes:
- When the pressure drops, the air mixed in the fluid can escape (this can happen at places like valves or where the fluid goes back into the tank).
- If the system isn’t correctly bled, air can get trapped and create bubbles.
- Leaks in the suction line can pull in the air, causing bubbles.
- Some chemicals can stop the fluid from releasing air properly.
- When fluid splashes into the system, it can trap air and form bubbles.
- Poorly designed tanks can also trap air.
Bubbles can form when the system pressure drops, like at valves or small openings. If a valve is suddenly opened, it can cause a rush of air, creating bubbles. When a pump stops suddenly, it can cause shockwaves that make bubbles.
What Causes Hydraulic Oil to Foam?
If your hydraulic oil is foaming, here are some reasons why:
- Water, dirt, or grease might have gotten into the fluid.
- The wrong type of fluid might have been used.
- Too much air is in the fluid, which is often a mechanical problem.
- The pump might not be working well.
- Even if you’ve used a defoamant before, it might only work if you’ve used less or if it’s run out.
Static Pressure Decrease
When the fluid temperature increases or the static pressure goes down, the air in the fluid can’t stay mixed, and bubbles start to form. This can happen at the pump inlet if there are issues like:
- Clogged suction filters
- Small or clogged breathers in the reservoir
- Blocked intake lines
- Turbulence from valves in the intake line
- Badly designed inlets
- There is too much distance between the pump intake and the fluid level
Changes in fluid speed, sudden changes in flow, or broken valves that control pressure can also lower static pressure.
Air can also get into the system from outside. This can happen because of:
- Loose clamps or fittings on the intake line
- Leaky intake lines
- Low fluid levels in the reservoir
- A broken shaft seal on the pump
- Faulty valves that let air in through the cylinders
To fix this, ensure return pipes stay above the minimum fluid level in the reservoir. Regular maintenance is essential because it helps stop these problems from happening in the first place.
How to Prevent Air from Contaminating Hydraulic Oil
Hydraulic oil can get damaged when air gets mixed into it. Air is a contaminant, which means it can mess up how the oil and the hydraulic system work.
There are four ways air can be in the oil:
- Dissolved Air: Hydraulic oil usually has 6% to 12% air mixed in with it.
- Entrained Air: Tiny air bubbles, smaller than a millimeter, get mixed into the oil.
- Foam: Larger air bubbles gather at the top of the oil and create foam.
- Entrapped Air: This is the most complex type of air to deal with. Free air can usually be removed during startup by filling parts and bleeding the system. A little foam is usually not a problem, but if there’s a lot of foam, it can mean there’s a more significant issue with air contamination or oil damage.
It’s essential to regularly check and maintain the system to prevent air from contaminating the oil.
Bottom Line
Foaming hydraulic fluid can cause serious problems, like less lubrication and faster fluid damage. Choosing the proper hydraulic fluids that help prevent foaming and air contamination is essential to fix this.
At Fubex, we offer excellent options to keep your hydraulic system working well. Explore all our products or contact our team for helpful advice.
FAQs
Q1: What are the effects of air entrainment?
Ans: Air entrainment in concrete makes it a little less intense but much more durable, lasting up to 60 times longer, depending on the amount of air and the type of rocks used.
Q2: What is air entrainment in hydraulic fluid?
Ans: Air entrainment happens when air bubbles mix with hydraulic fluid. These bubbles weaken the fluid’s ability to carry pressure, which can make the system work less efficiently.
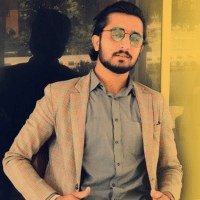
Editor-at-Large
A passionate writer in the lubricant industry, Awais Iqbal has been covering oils, greases, and industrial fluids since the start of his career. At 25, he’s already written for blogs, catalogs, and brand guides across the UAE. Awais’s insights help companies connect with their audience, and his clear, helpful writing style is trusted by brands in the region.