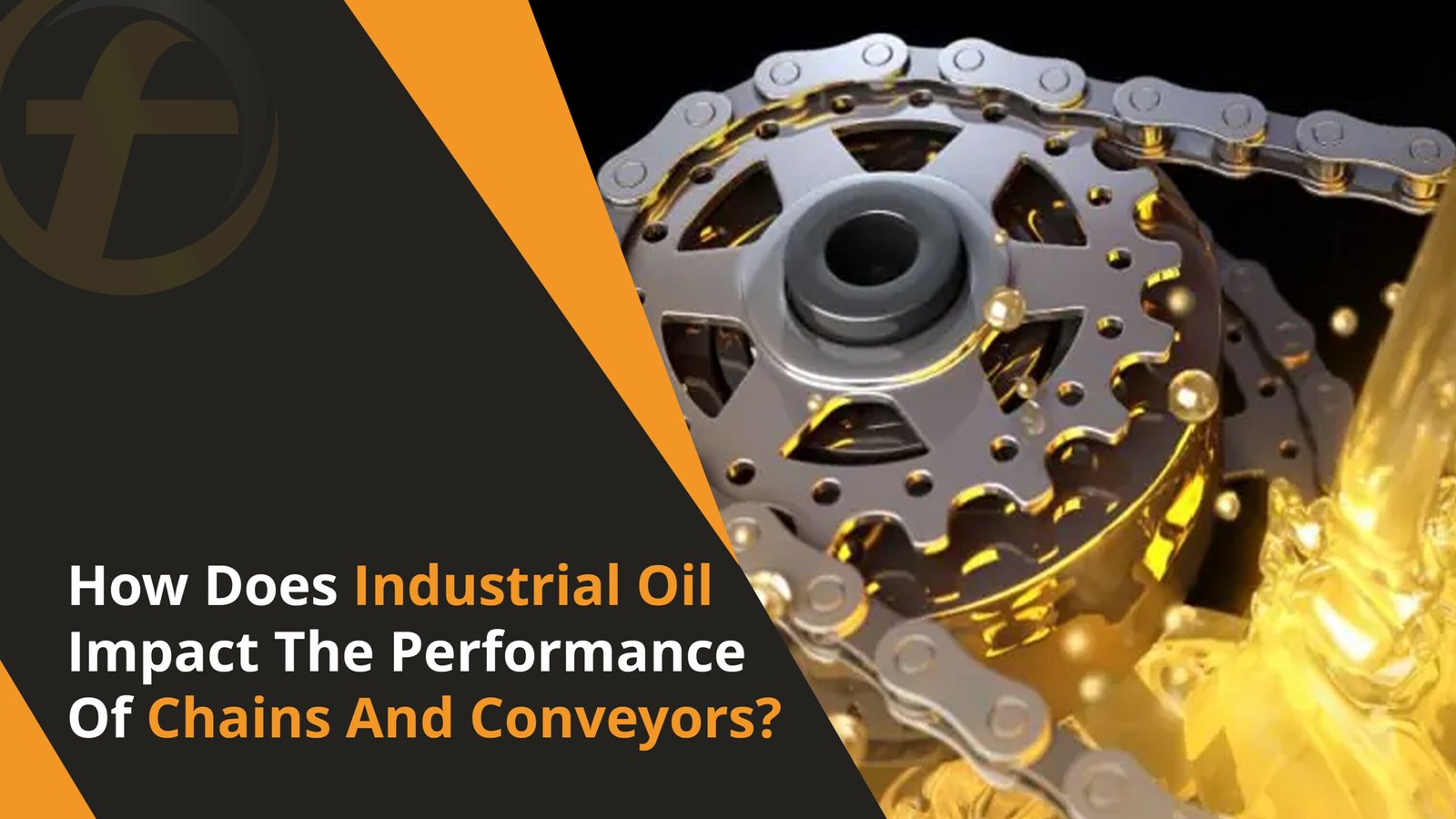
Chains in drives and conveyors work hard and face harsh conditions like high heat, heavy loads, and lots of dust. They can get very hot and often rub against each other, causing friction. We need to use lubrication to help them work better and last longer.
Lubrication is like a protective layer that helps the chains move smoothly. If there isn’t enough lubrication, the chains can wear out quickly, make loud noises, rust, or even break. This can cause problems with production.
To keep chains working well, we need to lubricate them regularly. Using the correct type of lubricant helps keep the chains in good shape. Suitable lubricants can reduce friction and clean away dirt, which allows the chains to work smoothly and last longer.
Next, we’ll dive into an example that shows how proper lubrication enhances the reliability of conveyor chains in high-temperature environments.
Role of Industrial Oil In Maintaining Chains & Conveyors Systems
A chain conveyor system has a series of bearings connected by link plates, with pins and bushes on which the chain roller moves. These parts are constantly in motion, creating a lot of friction, making machines overheat and get damaged.
To prevent this, a thick layer of oil or lubricant is used between the metal parts to reduce friction. This helps the bearings and other parts run smoothly for a long time. The metal parts can wear out without lubrication, and the conveyor system can stop working correctly.
Most problems with conveyor chain systems happen because of poor lubrication. Oiling your machines and giving them enough lubricant helps the parts slide smoothly against each other instead of scraping.
In conveyor chain systems, oils or greases can significantly reduce friction, allowing the chain roller to move efficiently and keeping the machine running smoothly.
Types of Industrial Oils Used In Chains & Conveyors
Lubricants reduce friction between two surfaces, but not all lubricants work the same way. Because it seems easy, new workers or trainees often handle these tasks.
But it’s essential to use the correct type of lubricant for the right job, so knowing about different kinds of lubricants is helpful.
This ensures you don’t use the wrong kind, which can cause machines to break down or stop working. Plus, it helps you find trusted suppliers with the best quality products.
There are four main types of industrial lubricants:
- Oil
- Grease
- Penetrating lubricants
- Dry lubricants
The most common ones you’ll see are oil and grease, but sometimes, you might also need penetrating and dry lubricants. It’s important to know when to use each one.
How Industrial Oil Reduces Friction & Wear?
Lubricants help machines work better by reducing friction when two surfaces rub against each other. They create a thin layer between the moving parts, keeping the metal pieces from touching directly.
This helps reduce wear and tear on the machine. The most common lubricant is oil, but grease, solid, and liquid lubricants are also used.
Oil is the most used because it works well in many situations. It forms a thin film on metal surfaces that helps parts slide smoothly. Grease is like oil but is thicker and sticks better because of special additives.
Solid lubricants coat metal parts to make them slippery, and liquid lubricants are used when oil or grease won’t work, like in very high temperatures or fast-moving machines.
How Does Lubrication Help Conveyor Chains?
Lubrication helps conveyor chains last longer, sometimes up to 100 times longer! It reduces friction between moving parts, so they don’t wear out quickly. Lubrication also stops rust, protects against heavy impacts, and removes dirt and dust.
Ways to Lubricate Conveyor Chains
Manual Lubrication
This method means adding oil by hand using a brush, spray, or oil can. It’s cheap, but you need to do it almost every day. It can slow down work and might be dangerous if not done carefully.
Oil Bath Lubrication
Part of the chain moves through a basin of oil. The chain must be just the right amount in the oil—too much or too little can cause problems like rust.
Drip Lubrication
Oil drips slowly onto the chain at a few drops per minute. This keeps everything moving smoothly. The chain can rust if too much or too little oil is used. This works well for machines in tight spaces, but you must avoid leaks.
Force-Feed Lubrication
This method uses a pump to spray oil onto the chain. It’s excellent for big, fast, and powerful machines. It costs more but works well.
Other lubricating ways include using oil rings, brushes, or oil sprays.
How to Lubricate a Conveyor Chain System?
A conveyor chain system comprises parts like bearings, pins, and links that are always moving. They run on a track with electric motors and need lubrication.
If the bearings don’t get enough lubrication or are overloaded, they can become loose and not work right. But if you lubricate the system regularly, it can last 10 to 20 years!
To lubricate the conveyor chain, you need the correct oil and grease. You might also use a brush that applies oil to the pins, bearings, and links. Knowing the oil’s viscosity is essential, which is how thick or thin it is.
Viscosity tells you how fast or slow the oil flows. It would be best to consider the temperature because hotter temperatures make the oil thinner.
Pick an oil thick enough to keep a protective layer on the needed parts. This will help the conveyor chain work well and last longer.
How to Make Your Conveyor Chain Last Longer?
Keeping your conveyor chain in good condition helps your assembly line work smoothly and safely for a long time. Here’s what can affect how long your conveyor chain lasts:
- Weight: The chain can wear out faster if it carries heavy loads.
- Environment: High temperatures or lots of moisture can make the chain wear out sooner.
- Maintenance: Regular care is critical.
Choose a chain that matches the weight and conditions it will face to make your conveyor chain last as long as possible. Please keep it away from harmful stuff and extreme temperatures.
Stick to a regular maintenance schedule to help your chain last longer. Chains can stretch out over time, so it’s a good idea to replace them when they stretch by 1.5 to 2 percent. If they stretch by 3 percent, they might damage other parts or cause big problems.
Regular lubrication and care can help reduce wear and make your conveyor system last even longer.
Bottom Line
Industrial oil is essential for keeping conveyor chains and machines working well. Machine chains deal with a lot of heat, heavy stuff, and dust, which causes friction. This friction can make the chains wear out fast if not immediately lubricated.
Like oil, lubrication helps create a layer between the moving parts. This reduces friction and keeps the chains from getting damaged. Without enough oil, the chains can rust, make noise, or even break, which can stop production.
Use the correct oil to make your conveyor chains last longer and keep up with regular lubrication. This helps reduce friction, clean away dirt, and protect against rust. Good lubrication keeps everything running smoothly and makes the chains last much longer.
Maximise the performance and longevity of your machinery with Fubex Industrial Oil – your solution for reducing friction and enhancing efficiency. Get yours today!
FAQs
Q1: What are the signs of insufficient lubrication in conveyor systems and chains?
Ans: If you don’t use lubrication, chains can get noisy and shaky because they rub together too much. Using the right oil or grease helps them run more smoothly and quietly.
Q2: How often should a conveyor be serviced?
Ans: You should check your conveyor every week or month. During these check-ups, fix common problems like the belt getting off track, slipping, or carrying stuff back.
Q3: What should you consider when picking the proper lubrication for your chain drive?
Ans: Consider a few things when choosing the proper lubrication for your chain drive. These include how hot or cold it gets where the chain is used, how fast it moves, the type of environment (if it’s duster wet), how much the lubrication costs, and any special needs you might have.
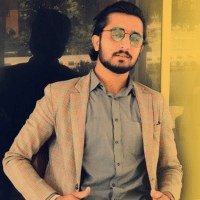
Editor-at-Large
A passionate writer in the lubricant industry, Awais Iqbal has been covering oils, greases, and industrial fluids since the start of his career. At 25, he’s already written for blogs, catalogs, and brand guides across the UAE. Awais’s insights help companies connect with their audience, and his clear, helpful writing style is trusted by brands in the region.