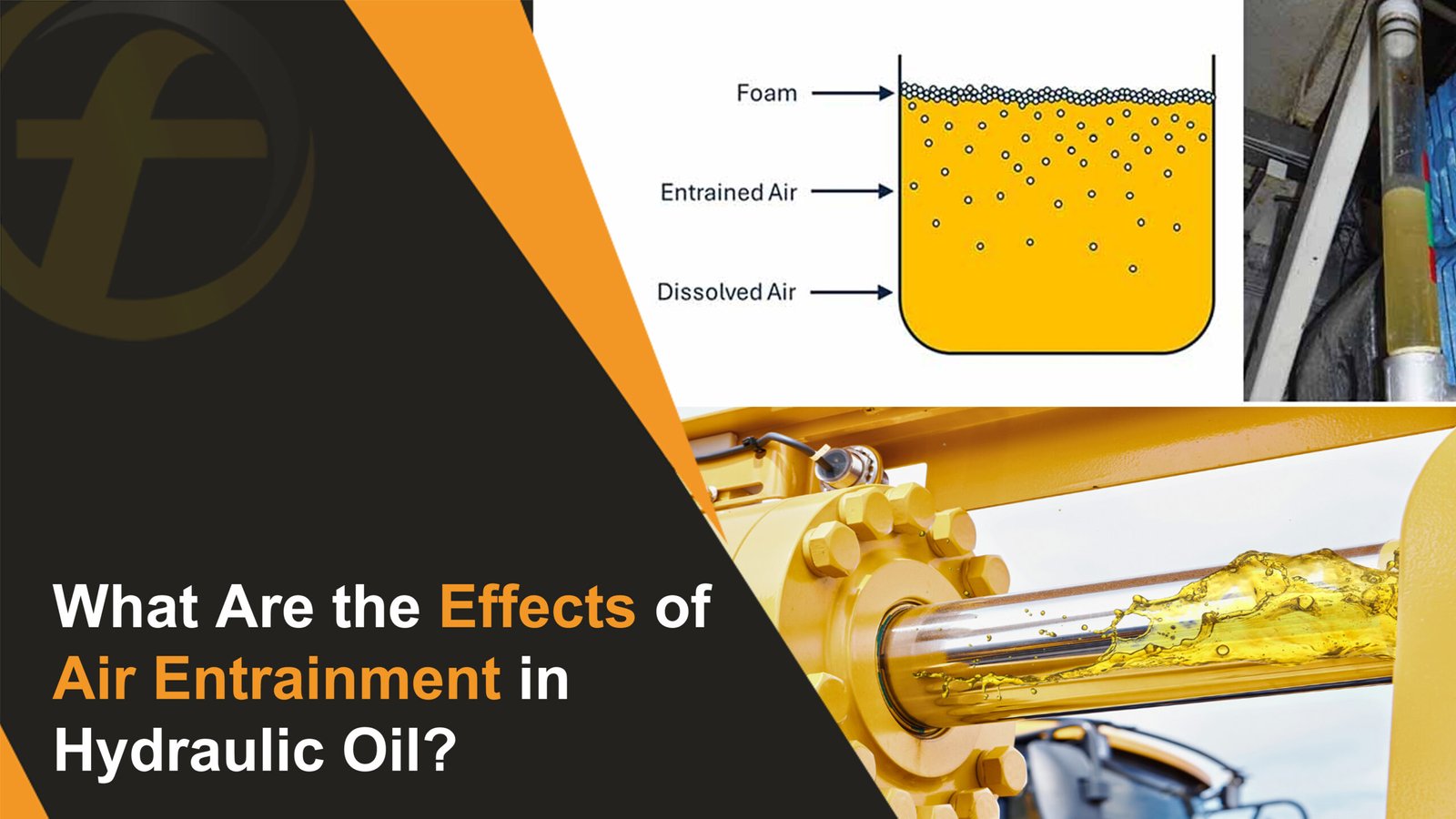
Air contamination is a common problem in hydraulic systems that can cause them to not work properly. When air gets mixed into the hydraulic fluid, it can slow down the system, make it noisy, and even cause damage.
Air can enter the system in different ways, such as bubbles trapped in the fluid or dissolved air. Understanding how air affects the hydraulic system and how to prevent it can help it run smoothly and safely.
Air Contamination in Hydraulic Systems
Air contamination is a common problem in hydraulic systems. It happens when air gets into the hydraulic fluid and causes the system not to work as it should. Air in a hydraulic system can show up in four ways:
- Dissolved Air: Hydraulic fluid always has a small amount of air mixed in, usually 6-12% by volume.
- Free Air: This is air trapped in pockets inside the system. You can eliminate free air by filling parts properly and removing air bubbles during start-up.
- Foam: Foam comprises bigger air bubbles (over 1mm) that gather atop the fluid. Small amounts of foam usually don’t cause problems.
- Entrained Air: These are tiny air bubbles (less than 1mm) spread throughout the fluid.
Entrained air is the most harmful because it can cause:
- Loud noises in the system.
- Slow or squishy responses from the hydraulic parts.
- Less slippery fluid, which makes parts wear out faster.
- The extra heat can damage the system.
- Fluid breaking down can lead to leaks and worn-out seals.
- Cavitation, which means tiny bubbles explode and harm the parts.
- The whole system is becoming less efficient.
Check for air contamination regularly to keep a hydraulic system working well. Use good-quality hydraulic fluid and perform proper maintenance to avoid these issues.
Why is Air in Hydraulic Systems a Problem?
Air in a hydraulic system can cause problems because it slows everything down and makes the system feel “spongy.” This happens because air can be squeezed (compressed), but hydraulic fluid cannot.
Here’s how it works:
- When you use the control valve to move something, the air must be squished before the fluid can do its job, slowing the system’s response.
- When you stop using the control valve, the squished air expands and keeps the system moving, even though you don’t want it to.
This wastes energy and makes the system less efficient. It can also be dangerous if you can’t control the movement, causing accidents.
Air can also make the system noisy, shaky, and more complicated, especially when starting it up. These problems might upset customers and make the system less useful.
To keep a hydraulic system working safely and efficiently, it’s important to remove air and prevent it from entering.
What is Cavitation Damage?
Cavitation happens when tiny bubbles form in a liquid and then pop quickly because of pressure changes. These bubbles appear in low-pressure areas and burst when the pressure increases, making powerful shockwaves.
This can cause severe damage to things like hydraulic equipment, machines, and propeller blades. For example, cavitation can even hurt fish fins when they swim fast, but their fins can heal. Machines, however, cannot!
How to Tell If Air Is in the System
- Foam – Bubbles or foam on top of the fluid can mean there’s air in the system.
- Loud Noises – Extra air in the fluid (called aeration) or cavitation can make strange or loud noises. This happens when air gets into the fluid, or the fluid level is too low.
- High Pressure – Small hoses or pipes can block fluid flow, causing pressure to build up. This can be fixed by using wider hoses and draining the system to remove blockages.
Hydraulic fluid always has a little dissolved air, up to 12%. But this air can turn into tiny bubbles under certain conditions, causing gaseous cavitation.
To avoid cavitation damage, always check fluid levels, use the right-sized hoses, and ensure air stays out of the system.
Why Is Entrained Air Bad?
Entrained air means tiny bubbles are stuck in hydraulic fluid, and this can cause a lot of problems, such as:
- Spongy feel – The system doesn’t respond quickly and is more challenging to control.
- More heat – The system heats up faster, which can damage parts.
- Insufficient cooling – The fluid can’t keep the system cool.
- Fluid damage – Air makes the fluid wear out quicker because of overheating and oxidation.
- Thinner fluid – The fluid gets too thin, leaving parts unprotected and more likely to wear out.
- Cavitation damage – Tiny bubbles pop and damage the system parts.
- Loud noises – The system gets noisier and less smooth to use.
- Less efficiency – The system doesn’t work as well as it should.
To keep your system running smoothly, it’s important to remove air and prevent it from entering the hydraulic fluid.
What is Gaseous Cavitation?
Hydraulic oil can hold a small amount of dissolved air, about 12%. But when things change, like the oil getting hotter or the pressure dropping, this air can turn into tiny bubbles. This is called gaseous cavitation.
Here’s when it happens:
- The oil heats up and can’t hold as much air, so bubbles form.
- The pressure drops, like near the pump, and the air escapes as bubbles.
At the pump inlet, cavitation can happen if:
- Filters or strainers are clogged, making the fluid’s flow harder.
- Valves cause turbulence – This mixes air into the oil.
- The inlet is too small or too long – Poor design can create problems.
- The intake line is damaged or collapsed, which blocks the flow.
- The pump is too far from the fluid – If the pump has to pull fluid from too high up.
- The breather is clogged, stopping air from flowing correctly into the reservoir.
Other causes include changes in how fast the fluid moves or valves that aren’t working right.
What is Air Ingestion?
Air can also sneak into the system from outside, which is called air ingestion. This happens when:
- Clamps or fittings are loose – Letting air leak in.
- Pipes are damaged – Air seeps through holes or cracks.
- The oil level is too low – Exposing parts to air.
- The pump seal is broken, allowing air to enter the pump.
Other problems, like valves not appropriately adjusted or oil splashing in the reservoir, can also let air in. To fix this, make sure return pipes go below the oil level.
By keeping the system sealed and well-maintained, you can stop bubbles and air from causing damage.
What Happens When Static Pressure Drops?
When the fluid gets hotter or the pressure drops, air that’s mixed into the fluid can start to form bubbles. This usually happens near the pump and can be caused by:
- Clogged filters or strainers – Stopping the fluid from flowing smoothly.
- A slight or clogged breather – Not letting air move properly.
- A blocked intake line – Preventing the fluid from flowing freely.
- Turbulence from valves – Mixing air into the fluid.
- Poorly designed pump inlet – If it’s too small or long.
- Too much height – If the pump is too far above the fluid.
Other causes can include changes in how fast the fluid moves or valves that are not set correctly.
Air Getting Into the System
Sometimes, air can get into the system from outside. This happens when:
- Clamps or fittings are loose – Letting air in through the pipes.
- Pipes are damaged – Allowing air to sneak in.
- The fluid level is too low – Exposing the system to air.
- The pump seal is broken – Letting air inside the pump.
It can also happen when valves aren’t working right, causing air to enter through cylinders or splashing fluid back into the reservoir. To prevent this, make sure return pipes go below the fluid level.
How to Avoid Problems
It’s always better to fix problems before they happen. Keeping your hydraulic system and equipment well-maintained will help avoid air problems and keep everything running smoothly.
Bottom Line: What Are the Effects of Air Entrainment in Hydraulic Oil
To sum up, air in hydraulic systems can cause many issues, like slower operation, more noise, and damage to the equipment. Regular maintenance, using good-quality hydraulic fluid, and fixing any air problems quickly can help prevent these issues.
By understanding how air enters the system and how to manage it, you can keep everything running smoothly and avoid expensive repairs. Proper care is the best way to ensure your hydraulic system lasts longer and works efficiently.
At Fubex Lubricant, we offer high-quality hydraulic fluids that help prevent air contamination and keep your system working efficiently. Don’t wait for problems to arise—regular maintenance and using the right fluid can save you money in the long run. Contact us today to ensure your hydraulic system operates at its best!
FAQs
Q1: How can you stop air from getting into a hydraulic system?
To prevent air from entering the system, fill and bleed it before starting. Fix any leaks and ensure the oil level is high enough to keep air out of the pump.
Q2: How can you reduce oil aeration?
You can use filter material as a screen to help reduce the amount of air in the oil. However, this method can lower pump efficiency because it restricts the pump’s inlet.
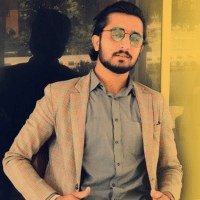
Editor-at-Large
A passionate writer in the lubricant industry, Awais Iqbal has been covering oils, greases, and industrial fluids since the start of his career. At 25, he’s already written for blogs, catalogs, and brand guides across the UAE. Awais’s insights help companies connect with their audience, and his clear, helpful writing style is trusted by brands in the region.